تضامنًا مع حق الشعب الفلسطيني |
زجاج
زجاج |




الزجاج هو مادة صلبة غير عضوية، عادة ما تكون شفافة أو نصف شفافة، صلبة، سهلة الانكسار، غير نافذة للمواد الطبيعية. بالرغم من أنه استعمل منذ القدم إلا أنه لا يزال مهم جدا في استعمالات شتى، مثل المباني والأدوات والأواني المنزلية ومعدات الاتصالات السلكية. وتختلف أنواع الزجاج اختلافا شاسعا باختلاف مكوناتها وخصائصها الفيزيائية. وأما أكثر أنواع الزجاج شيوعاً عبر العصور، وخاصة في عصرنا هذا، هو ذاك المستخدم في صناعة النوافذ وأواني الشرب، وهو زجاج صودا الجير، والذي يتكون من 75% من السيليكا وأكسيد الصوديوم وأكسيد الكالسيوم؛ مع أو بدون مضافات الأخرى.
لمحة تاريخية
الفراعنة
من زمن الفراعنة إلى اليوم، فإن (الخرز الزجاجي) المصري هو أقدم الأجسام الزجاجية المعثور عليها والتي يرجع تاريخها إلى حوالي 2500 سنة قبل الميلاد. لاحقا في الحضارة المصرية كذلك صنعت أواني زجاجية بها خطوط ملونة، متوازية مسننة في بعضها وذات طابع ريشي في الآخر.
الرومان
وقد تمكن الرومان من صب زجاج النوافذ، دون أن يكون بالصفاء الكافي، ولم يزد استخدامه عن السماح بدخول الضوء، دون التعرض للظروف الجوية. وكان الزجاج يُصبَّ على هيئة لوح مسطح، وربما أجريت عليه عملية درفلة وهو ساخن، لكي يصبح أرق سمكاً. وعلى الرغم من وجود الزجاج في عدد قليل من الكنائس القديمة، التي يرجع تاريخها إلى القرن السابع، إلا أن الألواح المتسعة من الزجاج الشفاف، لم تصبح شائعة إلا في القرن السابع عشر.
العرب
اعتنى العرب في العصور الوسطى بصناعة الزجاج وتطويره، فقد كانت الزخرفة تنفذ بأساليب مختلفة، منها طريقة الضغط على الأواني وهي لا تزال لينة، وكذلك بطريقة الملقاط، أو بطريقة «الإضافة» وهي تتم بلصق خيوط من الزجاج على جدران الأواني وهي لينة، أو لصق حامل من الزجاج الذي لا زال ليّنا، وربما يكون ملونا، وغيرها من الطرق الأخرى. ومن آثار صناعة الزجاج عند العرب القدامى، هي المجموعات المختلفة من القرن الثاني أو الثالث هجري، التي كانوا يصنعون منه الإبريق الزجاجي المصنوع بالطريقة الرومانية من القرن الثاني الهجري، وهذا القدر المزخرف بطريقة «الإضافة» من الدولة الفاطمية في القرن الخامس الهجري، وهذا إبريق من القرن الثالث الهجري من مصر، وهذه المزهرية من عصر المماليك. وقد زودت فوهتها بخيوط زجاجية ملونة، أما هذه القنينة فلها بدن مضلع ونفّذت بالقالب وزخرفت رقبتها بإضافة خيوط زجاجية من القرن الثامن الهجري.وهذا جزء من إناء فاطمي العصر زُخرف بالكتابة الكوفية مع الكائنات المتقابلة من القرن الخامس الهجري، أما هذه القنينة وتلك المكحلة فمن البلور الصخري، وقد زخرفتا بالقطع والشطف في مصر الفاطمية خلال القرن الخامس الهجري. والبلور هو زجاج مضافا إلى خلطته عناصر ثقيلة مثل الكوبلت ويتميز بكثافة عالية.وهذه بعض المكاييل الزجاجية المخصصة للعطور أو السوائل الطبية من القرن الثاني الهجري من عهد الأمويين، كما صنع العرب الموازين والصِنَج من الزجاج أيضًا، فهذا ثقل ميزان يوازي رطلاً ويرجع إلى عام 129 للهجرة. وهذا مثقال فلس من العصر الأموي المبكر، أما هذه الصِنَج فمن عهد «العزيز بالله» الخليفة الفاطمي، وهذا الثقل من عهد السلطان قايتباي عام 893 للهجرة.كما برع العرب في صنع المشكاوات؛ وذلك لإضاءة المساجد والمنازل وخلافه، منها عدد من المشكاوات المملوكية العصر المموهة بالمينا والمزخرفة بكتابة النسخ وكذلك عليها زخرفة نباتات. وهذه المشكاة باسم السلطان «حسن» وقد موهت بالمينا، وزخرفت بكتابات نسخية قرآنية وزخرفة نباتية فنية. وهذه من عهد السلطان «حسن»، وقد زخرفت فقط بزخارف نباتية دقيقة.و هذه المشكاة باسم الأمير «شايخو» ساقي السلطان المملوكي الناصر "محمد بن قلاوون"، وتضم مع الكتابة النسخية «رنك الكأس» الذي يشير إلى وظيفة الساقي؛ حيث تعتبر «الرنوك الوظيفية» سمة من سمات العصر المملوكي.واستخدم العرب الزجاج في زخرفة النوافذ أيضًا؛ حيث صنعوا الزجاج المعشق في الجص. وتمر هذه الصناعة بعدة مراحل؛ بداية برسم الوحدات الزخرفية على الجص، ثم تبدأ مرحلة التفريغ أي التخريم لهذه الوحدات المراد تعشيقها بالزجاج. وأخيرًا تبدأ مرحلة تركيب القطع الزجاجية المختلفة الأحجام والألوان من الخلف وتثبت بالجص السائل.وما زالت هذه الطريقة متوارثة لانتاج لوحات زخرفية متنوعة الأشكال تُشع من الضوء مثل نوافذ العمائر الإسلامية المختلفة. كما استخدمتها الكنائس في مصر أيضا للتزيين وصناعة النوافذ الملونة. كما استخدم العرب الزجاج في عمل زخارف الفسيفساء؛ مثل الجامع الأموي بدمشق الذي تضم زخارفه مناظر طبيعية بديعة.
صناعة الزجاج
يمكن تقسيم الزجاج إلى نوعين هما؛ العادي أي زجاج الصودا والجير والسيليكا، والزجاج النوعي، فالزجاج العادي هو الأكثر إنتاجا ويتكون من الرمل (أو السيليكا التي هي أكثر نقاوة من الرمل) والجير والصودا.
والسيليكا المنصهرة وحدها تنتج زجاج ممتاز، لكنها تنصهر عند حوالي 1700 درجة مئوية أي أن إنتاج الزجاج بهذه الطريقة مكلف، لذلك فهذه الطريقة تقتصر على إنتاج الزجاج المتوجب فيه درجة أفضل من الخمول الكيميائي والقدرة على تحمل الصدمات الحرارية أو في إنتاج أغراض البصريات وتستعمل الصخور الكريستالية بدل كوارتز الرمل لإنتاج هذا النوع.
أما في حالة الزجاج العادي فان السليكا (أو الرمل) يضاف إليها مُسهّل صهر لتخفيض درجة الحرارة اللازمة لصهر المزيج، لهذا فإن الصودا تستعمل لتسهيل الصهر حيث أنه بإضافة 25 بالمئة من الصودا إلى السيليكا تكون درجة انصهار المزيج عند 850 درجة مئوية بدل 1700 درجة مئوية، لكن الزجاج الناتج منهما لا يصمد في الماء بل يذوب ولذلك يسمى زجاج الماء، وهنا يكمن دور إضافة الجير، فبإضافة الجير إلى مزيج السيليكا والصودا نحصل على زجاج لا يذوب في الماء بينما تكون درجة حرارة صهر المزيج ليست عالية جدا، لكن إضافة كمية كبيرة من الجير تجعل الزجاج الناتج سهل التفتت.
مكونات الزجاج العادي (زجاج سيليكا صودا جير):
- 75 % سيليكا (اكسيد السيليكون)أو رمل
- 15 % صودا (كربونات الصوديوم (ملح القلي) أو (اكسيد الصوديوم)، أو بورق (بوتاس)
- 10 % الجير(حجارة كلسية أي حجارة الجير كربونات الكالسيوم أو الجير الغير مطفى: أكسيد الكالسيوم)
بالرغم من هذه الوصفة المتبعة في إنتاج الزجاج اليوم إلا أنه يبقى عرضة إلى التفتت خلال عملية تشكيله.
لصنع الصفائح الزجاجية من العادة يستخدم 6 في المئة من الجير و 4 في المئة من المغنيسيا (أكسيد المغنيسيوم، MgO)، أما لصنع زجاج القوارير يستخدم 2 في المئة الألومينا (أكسيد الألومنيوم، أو Al2O3) غالبا ما تكون موجودة. كما يتم إضافة مواد أخرى منها ما يتم وضعه للمساعدة في تصفية الزجاج (أي لإزالة فقاعات نتجت في عملية ذوبان)، في حين يتم إضافة غيرها لتحسين لونه. على سبيل المثال، الرمل يحتوي دائماً على الحديد كشوائب على الرغم من أن المواد المستخدمة لصنع الزجاجات يتم اختيارها خصيصا لانخفاض محتوى الحديد فيها، إلا أن بقاء آثار صغيرة من شوائبه يكسب الزجاج اللون الأخضر غير المرغوب فيه؛ لكن باستخدام السيلينيوم مع أكسيد الكوبالت جنبا إلى جنب مع قليل جداً من ثالث أكسيد الزرنيخ ونترات الصوديوم، فمن الممكن إزالة اللون الأخضر وإنتاج ما يسمى الزجاج الأبيض (الزجاج غير الملوّن).
أصناف الزجاج مختلفة جداً، وغالباً ما تكون أكثر تكلفة، تركيبات معينة تصنع لتلبي الحاجة لبعض الخصائص الفيزيائية والكيميائية الضرورية. على سبيل المثال، في النظارات البصرية، مجموعة واسعة من التركيبات تلزم للحصول على مجموعة متنوعة من معامل الانكسار والتشتت اللازمة. وللحصول على زجاج مقاوم للصدمات الحرارية يمكن صهر السليكا وحدها أو كبديل تستبدل الصودا بحمض البوريك في حين ستبدل بعض الجير بالألمونياAlO3 فينتج ما يسمى البورو سلسيكات. أمّا للحصول على زجاج ذو بريق شديد كالذي يستعمل في أواني الطاولة فيستعمل أكسيد الرصاص كمّسهّل صهر للسيليكا[1]
تشكيل الزجاج

تتضمن العمليات الأولى لتشكيل الزجاج: صب لوح من الزجاج ثم درفلته وصقله، أو نفخ كرة من الزجاج، ثم تدويرها في حركة مغزلية على طرف قضيب مع إسنادها على سطح أملس بارد حتى تتسطح على هيئة قرص أو تأخذ شكل الأسطوانة، وصقله بواسطة اللهب وتنعيم سطحه. ولصناعة أكواب فيتم بإدخال كرة الزجاج التي لا زالت منصهرة في قالب وتدويرها فيه فتأخذ شكل القالب ثم تبرد. بعد إزالة الطرف يصبح الكوب جاهزاً.
واحتاج عمليات التزجيج (صناعة الزجاج) القديمة، إلى أطر صغيرة للنوافذ، لتركيب هذا الزجاج (التاجي) أو (النورماندي) عليها، وظل بعضها محتفظاً بـ (عين الثور) المميزة في مركزها، كعلامة مختلفة عن استخدام القضيب. أما العملية البديلة لإنتاج (الزجاج العريض) فكانت تعتمد على أرجحة الكرة، حتى تتمدد وتتحول إلى شكل أسطواني، يصل طوله إلى حوالي متر ونصف، بقطر حوالي 45 سم. ثم تزال الأطراف وتشق الأسطوانة على طولها، ثم يتم تسطيحها في فرن مناسب.
وظلت الطريقة الأخيرة، مع طريقة أخرى متطورة عنها تعتمد على الميكنة، قيد الاستخدام حتى أوائل القرن العشرين، حين تم التوصل إلى طريقتين أخرتين هامتين:
طريقة بيترسبرج
طريقة (فوركو) عام 1904 وطريقة (بتسبرج) عام 1926 وتعتمد كلتا الطريقتين على سحب شريط من الزجاج رأسيّاً من فرن الزجاج، عبر فرن تلبيد (تلدين) بواسطة درافيل من الاسبستوس تدار بالمحركات، تقوم بمسك الشريط من طرفه العلوي بمجرد برودته لدرجة كافية، بعد عدة أقدام أعلى الفرن. وتسمح عملية التلدين بتبريد الزجاج ببطء بمعدل محدد، ويعد التبريد ببطء أمراً ضرورياً لتجنب الإجهادات الناشئة عن التبريد السطحي السريع. ويتميز الزجاج الناتج بشفافيته، وسطوحه المصقولة الصلبة، مع وجود بعض التشوه أو العيوب.
وكان الحصول على لوح زجاج مصقول فيما سبق من طرق، يتم بدرفلة الزجاج المصهور من الفرن، على هيئة شريط مستمر، ولكن كان يعيب ألواح الزجاج، وجود علامات (ندبات) بسطحه، نتيجة التلامس بين الزجاج والدرافيل. لذلك كان يتحتم إزالة هذه العلامات بالتجليخ والصقل بغرض الحصول على سطحين متوازيين للوح الزجاج لتحقيق الاكتمال البصري (الخواص الضوئية الجيدة) للمنتج النهائي. وبالطبع، يتخلف عادم يقدر بحوالي 20% من عمليات التجليخ والصقل، كما كان من الصعب في الماضي إخلاء الزجاج من الفقاقيع الهوائية.
أسلوب الطفو
منذ ظهور عملية الطفو على يد شركة (بيلكنجتون) البريطانية عام 1959 أصبحت الطريقة الأساسية المستخدمة في العالم أجمع لتصنيع الزجاج المسطح، وكان يتعين قبل ذلك، صب أي لوح مسطح من زجاج، ثم درفلته وصقله للتخلص من الإعوجاج وعدم الاستواء.
ويعتمد أسلوب الطفو على تحريك شريط من الزجاج بعرض يصل إلى 33 متراً إلى خارج فرن الصهر، ثم يتم تعويمه على سطح حمام (مغطس) من مصهور القصدير. ويحتفظ بالشريط في جو يتم التحكم في تركيبه الكيميائي، عند درجة حرارة مرتفعة، لمدة زمنية كافية لاستواء المواضع غير المنتظمة، وحتى يصبح السطحين مستويين ومتوازيين. ويتميز سطح الزجاج الناتج بالاستواء التام، نتيجة الاستواء المماثل لسطح حمام القصدير المنصهر.
ويجري تبريد الشريط مع تحركه عبر حمام القصدير المنصهر، حتى تتصلد السطوح بدرجة كافية لإمرار الشريط، عبر مرحلة التلبيد، دون أن تترك الدرافيل علامات (ندبات) على السطح السفلي للشريط، ويتميز الزجاج الناتج بهذه الطريقة بانتظام السُمْك ولمعان سطوحه، دون حاجة إلى تجليخ أو صقل.
وبعد مرور سبع سنوات من العمل المضني، وبعد 14 شهراً من التشغيل غير الناجح لمصنع أُقيم بالحجم الصناعي الكامل، وتكلف مائة ألف من الجنيهات الإسترلينية، كل شهر من هذه الشهور، ظَهرت أول ألواح زجاجية ناجحة، ثم تصنيعها بهذه الطريقة، بثخن 6 ملم. وقد تحدد هذا السُمك بطريقة تلقائية، نتيجة القوى الطبيعية المؤثرة على حمم الطفو، وهي ظاهرة حسنة، إذ يحتاج 50% من سوق الزجاج مرتفع الجودة، إلى هذا السُمك.
ولكن الاستفادة الكاملة من طريقة الطفو، اقتضت السيطرة والتحكم في سُمك الشريط المنتج، وهو أمر أولته شركة (بيلكنجتون) اهتمامها، إلى أن تمكنت بعد عامين من ظهور هذه الطريقة من إنتاج زجاج بسمك 3 ملم وتحقق ذلك عن طريق مط الشريط برفق، وبطريقة يتم التحكم فيها، بحيث انتفى وجود أيّة تشوهات في الألواح الناتجة.
ثم أمكن إنتاج ألواح أكثر سمكاً خلال السنوات الثلاث التالية، عن طريق الحد من الاستطالة التي يتعرض لها الزجاج المصهور في حمام الطفو، حتى تتاح زيادة السمك، ويبلغ مدى السمك المتوافر حالياً من 4 ملم حتى 25 ملم من الزجاج المناسب لأغراض البناء، وسمك 2.5 ملم لأغراض أخرى.[2]
صناعة الزجاج عند العرب
اعتنى العرب في العصور الوسطى بصناعة الزجاج وطوروها لحاجتهم إلى الأواني الزجاجية التي تستخدم في العطور، والعقاقير، والإنارة، والشرب، وغيرها. وكانت الزخرفة تنفذ بأساليب مختلفة منها طريقة الضغط على الأواني وهي لا تزال لينة، وكذلك بطريقة الملقاط، أو بطريقة «الإضافة» وهي تتم بلصق خيوط من الزجاج على جدران الأواني وهي لينة، أو لصق حامل من الزجاج الذي لا زال ليّنا، وربما يكون ملونا وغير ذلك من الطرق الأخرى.
ولقد صنع العرب القدامى أنواعاً كثيرة من الأواني الزجاجية؛ منها هذه المجموعة المختلفة الأشكال التي ترجع إلى القرن الثاني أو الثالث الهجري. هذه آنية زجاجية ترجع إلى القرن الثالث الهجري، وهذا الإبريق الزجاجي المصنوع بالطريقة الرومانية يرجع إلى القَرن الثاني الهجري من عصر الدولة العباسية، أما هذا القدر فقد زخرف بطريقة «الإضافة» في مصر الفاطمية خلال القرن الخامس الهجري، وهذا إبريق يرجع إلى القرن الثالث الهجري من الدولة العباسية، كما وصلتنا هذه المزهرية عصر المماليك. وقد زودت فوهتها البديعة الصنع بخيوط زجاجية ملونة، أما هذه القنينة فذات بدن مضلع ونفّذت بالقالب وزخرفت رقبتها بإضافة خيوط زجاجية وهي من القرن الثامن الهجري.
وهذا جزء من إناء فاطمي العصر، وقد زُخرف بالكتابة الكوفية مع الكائنات المتقابلة ويرجع إلى القرن الخامس الهجري، أما هذه القنينة وتلك المكحلة فمن البلور الصخري، وقد زخرفتا بالقطع والشطف في مصر الفاطمية خلال القرن الخامس الهجري. والبلور هو زجاج مضافا إلى خلطته عناصر ثقيلة مثل الكوبلت ويتميز بكثافة عالية.
وهذه بعض المكاييل الزجاجية المخصصة للعطور أو السوائل الطبية من القرن الثاني الهجري من عهد الأمويين، كما صنع العرب المسلمون الموازين والصِنَج من الزجاج أيضاً، فهذا ثقل ميزان يوازي رطلاً ويرجع إلى عام 129 للهجرة. وهذا مثقال فلس من العصر الأموي المبكر، أما هذه الصِنَج فمن عهد «العزيز بالله» الخليفة الفاطمي، وهذا الثقل من عهد السلطان قايتباي عام 893 للهجرة.
كما برع المسلمون في صنع المشكاوات؛ وذلك لإضاءة المساجد والمنازل وخلافه، منها عدد من المشكاوات المملوكية العصر المموهة بالمينا والمزخرفة بكتابة النسخ وكذلك عليها زخرفة نباتات. وهذه المشكاة باسم السلطان «حسن» وقد موهت بالمينا، وزخرفت بكتابات نسخية قرآنية وزخرفة نباتية فنية. وهذه من عهد السلطان «حسن»، وقد زخرفت فقط بزخارف نباتية دقيقة.
أمّا هذه المشكاة فباسم الأمير «شايخو» ساقي السلطان المملوكي الناصر "محمد بن قلاوون"، وتضم مع الكتابة النسخية الجميلة «رنك الكأس» الذي يشير إلى وظيفة الساقي؛ حيث تعتبر «الرنوك الوظيفية» سمة من سمات العصر المملوكي.
واستخدم العرب الزجاج في زخرفة النوافذ أيضاً؛ حيث برعوا في صناعة الزجاج المعشق في الجص. وتمر هذه الصناعة بعدة مراحل؛ بداية برسم الوحدات الزخرفية على الجص، ثم تبدأ مرحلة التفريغ أي التخريم لهذه الوحدات المراد تعشيقها بالزجاج. وأخيراً تبدأ مرحلة تركيب القطع الزجاجية المختلفة الأحجام والألوان من الخلف وتثبت بالجص السائل.
وما زالت هذه الطريقة المتوارثة تنتج لوحات زخرفية متنوعة الأشكال تُشع من الضوء، ويبدو ذلك جليا في نوافذ العمائر الإسلامية المختلفة. كما استخدمتها الكنائس في مصر أيضا للتزيين وصناعة النوافذ الملونة. كما استخدم العرب الزجاج في عمل زخارف الفسيفساء؛ مثل الجامع الأموي بدمشق الذي تضم زخارفه مناظر طبيعية بديعة، وتعتبر فسيفساء هذا المسجد أقدم نموذج للفسيفساء الزجاجية الإسلامية بعد قبة الصخرة.-
بنية الزجاج
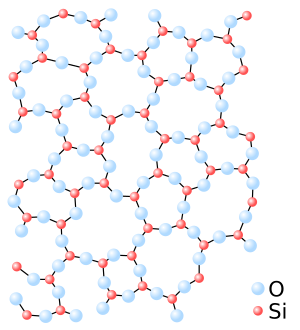
كما هو الحال في المواد الصلبة لا بلورية الأخرى فإن التركيب الأيوني للزجاج - وليس التركيب الذري لأن الزجاج لا يحتوي على الذرات - لا يحتوي أي تناظر انتقالي، ولكن نظراً لخصائص الترابط الكيميائي فإن الزجاج قد يمتلك درجة ما من الانتظام قصير المدى نسبة إلى المضلعات الذرية الموضعية القريبة ولكنها لا تتواصل في الزجاج على المدى البعيد.
أنواع الزجاج
يمكن تقسيم الزجاج من حيث تركيبه الكيميائي إلى ثلاثة أنواع:
- زجاج الصودا والجير: ويشكل ما يزيد عن 90% من الزجاج المستخدم: حيث يحتوي على أملاح الصوديوم وكربونات الصوديوم بنسبه عالية.
- الزجاج الرصاصي الكريستال: وهو زجاج براق، عالي الكثافة وذو معامل انكسار عالي للضوء، يستخدم في صناعة التحف والإكسسوارات والثريا وكان يستخدم قديما في حفظ الطعام والشراب ونظراً لتفاعل الرصاص مع المواد الغذائية توقف استخدامه لخطورته على صحة الإنسان.
- الكوارتز (زجاج السيليكا): ويحتوي على السيليكا بنسبه96% مما يجعله يحتاج إلى درجات حرارة عالية لتصنيعه، يتميز بمقاومة عالية لدرجات الحرارة، مما يجعله مناسباً لصناعة موازين الحرارة والأفران.
كما يمكن تقسيم الزجاج أيضاً من حيث المعالجة الفيزيائية إلى نوعين:
- الزجاج الملدن:
- الزجاج المُقسّى: حيث يسخن إلى درجة حرارة معينة ثم يبرد بشكل سريع عن طريق تعريض سطح الزجاج لتيارات هواء بارد. لذا فهو يتميز عن الزجاج الملدن العادي بما يلي:
-*يمكن للزجاج المقسّى تحمل صدمات ميكانيكية أشدّ ممّا يتحمله الزجاج الملدن العادي بـ 5 - 7 مرات. وعندما يتكسر الزجاج نتيجة صدمة شديدة، يتحول إلى عدد كبير من الشظايا صغيرة التي لا تجرح ولا تؤذي أحداً (لهذا السبب يسمى هذا الزجاج زجاج أمان مُقسّى). وخلافا للزجاج المقسى، فإن الزجاج العادي يتناثر عند تكسره إلى شظايا حادة جارحة بالغة الضرر.
-* كما يمكن للزجاج المقسَّى تحمل فرقا كبيرا بين درجات الحرارة الداخلية والخارجية، تصل إلى 300 درجة مئوية، في حين لا تتجاوز هذه الفروق 70 درجة مئوية في الزجاج العادي الملدن، مما يعرضها للكسر مباشرةً.
ومن الطرق الشائعة لتصنيع الزجاج هي خلط كمية كبيره من الرمل مع كميات قليله من الجير والصودا، ومن ثم تسخينه إلى درجة حرارة عالية تزيد عل 1100 درجة مئوية، حتى يصبح عجينةً سائلةً عالية اللزوجة، يتم بعدها تشكيله بطرق آلية أو يدوية، ومن ثم يبرد ليكون زجاجاً.
ويعتبر زجاج الصودا والجير (الزجاج المسطح): هو الزجاج الأكثر شيوعاً واستخداماً، حيث يشكل نسبه تزيد عن الـ (90%) من إجمالي الزجاج المستخدم في العالم. أما زجاج البوروسيليكات وهو ما يسمى بزجاج البايركس والكيموكس فهو يحتوي على السيليكا بنسبة (80%) وعلى القلويات بنسبة (4%) وعلى الألمونيوم بنسبة (2%) وعلى أكسيد البوريك بنسبة (13%). وهذا ما يعطيه الصلابة التي تزيد بثلاثة أضعاف الزجاج المسطح العادي.
أما زجاج السليكا المنصهر الكوارتز فهو يحتوي على السيليكا بنسبة (96%) ويتميز بمقاومته للصدمات، إلا أنه مرتفع الثمن.
وأهم خاصيّة للزجاج من ناحية تصنيعه هي لزوجته والتي تعتمد على درجة الحرارة، لِذا فإن زجاج السليكا النقي له لزوجه عالية ويحتاج إلى حرارة عالية جداً للتخلص من الفقاعات الموجودة فيه.
وهذا الشيء يجعل من صناعة زجاج السليكا النقي مكلف جداً. لذا ولأسباب علمية يلزم إضعاف زجاج السليكا لكي يسهل تصنيعه بشكل اقتصادي. ومن واقع الخبرة، يتضح أن اكسيدات المعادن القلوية هي خير وسيلة لتحقيق ذلك.
ويكمن السر في ذلك بأن كل ذرة سيليكون ترتبط بأربع ذرات فقط من الأوكسجين وأن أي ذرات إضافية من الأوكسجين تعمل خلخلة التشكيل المتماسك والقوي والمكون من سيليكون – أكسجين – سيلكون لذا أصبح من السهل تغيير تركيب زجاج السيليكا وجعله أكثر تحركاً وذلك باستخدام أكسيدات المعادن القلوية.
وتعتبر هذه أكسيدات المعادن القلوية من أهم عوامل الصهر المستخدمة في صناعة الزجاج، وأكثر هذه الأكسيدات استخداما هي الصودا التي تعتبر أرخصها ثمنا، وقد استخدمت أكسيدات معادن أخرى القلوية لهذا الغرض مثل (البوتاسيوم والليثيوم... الخ).
وهناك أنواع من الزجاج تستخدم في الصناعات الميكروية كالزجاج الحساس للضوء.
البرسبكـس
هو مكثور (polymer) الميثيل ميثاكريليت، اسمها التجاري (في الولايات المتحدة) هو «لوسايت»، كما يوجد له اسم تجاري آخر هو «بليكسي غلاس». ويتميز البليكسي جلاس بخواص بصرية ممتازة، وهي ملائمة لصنع النظارات والعدسات وعدسات الكاميرات. كما تستخدم في الإعلانات الضوئية الموجودة في الشوارع، ويصنع منها زجاجا شديد التحمل للصدمات بحيث يصلح لتأمين السيارات.
زجاج الأمان
رافق التطور التكنولوجي وبشكل دائم ما يسمى بعوامل الأمان التي من شأنها حماية العمال والعمل بآن واحد، والزجاج مادة خطرة ونتائج استخداماتها أثبتت خطورتها وخاصة أن الزجاج بشكل عام يتحطم إلى قطع كبيرة وحادة الأطراف قادرة على إيذاء الشخص كيفما كان وضع الحادث، لذلك كانت الغاية من زجاج الأمان هي تقليل خطورة الزجاج وجعله يتحطم على شكل أجزاء صغيرة وناعمة غير حادة ومتلاصقة دون أن تتناثر في أرجاء مكان الحادث.
ويصنع زجاج الأمان بإحدى طريقتين، وضع طبقة لدائنيه «بلاستيكية» رقيقة بين لوحين زجاجيين، أو تقوية ألواح الزجاج عن طريق معالجتها بالصدمة الحرارية. ولقد كان الكيميائي الفرنسي إدوار بنيديكتوس أول من صنع زجاج الأمان، وذلك حين ركب عام 1909 م رقاقة من السليولويد بين لوحين من الزجاج. وقد استخدم زجاج الأمان في الواجهات الواسعة التجارية وفي مجال واسع في عالم السيارات حيث كانت حوادث السير تحصد الكثير من الأرواح بسبب الزجاج.
اكتشاف زجـاج الأمان
أوقع العالم الفرنسي بينيديكتوس خطأ زجاجة تحتوي على مادة الكولوديون وهي مادة تستعمل لتضميد الجروح وللتصوير، من فوق الرف إلى الأرض، ولاحظ العالم أن الزجاجة قد تحطمت، ولكنها بقيت قطعة واحدة ولم تتفتت، فدهش للنتيجة، ولاحظ فضلا عن ذلك أن مادة الكولوديون تركت بعد أن تبخرت قشرة رقيقة على الزجاج، هي التي أبقته ملتحما بعضه ببعض.
وقرأ هذا العالم فيما بعد أن عدداً كبيراً من الإصابات تحدث بسبب تطاير شظايا زجاج السيارات الأمامي لدى حدوث حوادث الارتطام، وكانت السيارات وقتئذ في مستهل عهدها، فتذكر خطأه ومادة الكولوديون، فألفى فيها العلاج الناجع، ومذ ذاك، ظهر إلى الوجود الزجاج الأمين، غير القابل للكسر والتحطيم.
المركبات الموازنة في الزجاج
هناك عناصر ومركبات كيميائية ضرورية موازنة في عملية تصنيع الزجاج بأشكاله وأنواعه المعروفة بحسب الاستخدام، من أهمها:
1- الجير: هو عبارة عن كربونات الكالسيوم على شكل حجري ويضاف إلي الخلطة الزجاجية بعد طحنه لإكساب الزجاج بعض الخواص . ويستخدم جير الكالسيوم والدولوميت بكميات كبيرة مع الرمل وكربونات الكالسيوم.
2- أكسيد الرصاص: يعتبر من المكونات الرئيسية لأنواع الزجاج الظراني الذي يتميز بمعامل انكسار عال للضوء، وعادة ما تشتمل على نسبة كبيرة من البوتاس (يعطي للزجاج بريقاً ولمعاناً وفي نفس الوقت مقاوم للكهرباء والحرارة).
3- أكسيد البوريك: يخفض من درجة لزوجه السيليكا دون أن يزيد من تمددها الحراري، ومع إضافة كمية قليلة من أكسيد الألمونيوم يحافظ على شفافية الزجاج، ويجعله أكثر مقاوما للحرارة (البايركس)، وهي تستخدم في صناعة أدوات المخابز وأجهزة المختبرات والأنانبيب الصناعية لقدرتها على مقاومة التغيرات المفاجئة في درجات الحرارة وتحملها للمواد الكيميائية.
4- أكسيد الألمونيوم والجير: يستخدم هذا الخليط بنسبة كبيرة في الزجاج مع (10%) من أكسيد البوريك وقليل من القلويات لصناعة الزجاج الليفي.
بشيء من التقريب يمكن القول أن الزجاج هو خلطة مناسبة من الرمل (السيليكا) مع بعض الاضافات الكيميائية وبظروف حرارية معينة نحصل على تلك المادة العجينية التي تبرد لتعطينا الزجاج، والزجاج من أكثر المواد فائدة في العالم. وهو يصنع بشكل رئيسي من رمل السيليكا والصودا والجير.
ويمكن الحصول على خواص مختلفة للزجاج بحسب طريقة تحضيره ومكوناته حيث يمكن للزجاج أن يشكل بحيث يستخرج على شكل خيوط رفيعة جداً تستخدم في تصنيع الألياف البصرية، أو يمكن أن يشكل من الحالة العجينية ويكسب مطواعية ليسكب في قوالب تعطيه الشكل النهائي كمرآة التلسكوب التي يصل وزنها عدة أطنان، ويمكن أن تزاد صلادته أو قساوته ليصبح أقوى من الفولاذ وأكثر هشاشة من الورق مع إمكانية الحصول عليه بألوان وأشكال كثيرة.
الزجاج المعدني في خدمة المستقبل
أصبحت الحاجة إلى استخدام الزجاج المعدني ضمن المحولات الكهربائية ومضارب الغولف وضمن تطبيقات أُخرى أمراً مُلحا، الأمر الذي دفع «تود هاف نايغل» الباحث الجامعي في جامعة جونز هوبكنز وبروفسور علم المواد والهندسة، إلى البحث عن تركيبة زجاج معدني جديد يتميز بخصائص القوة والمرونة وخصائص مغناطيسية.
ويعرف علماء الزجاج أن أي مادة يمكن تحويلها من الحالة السائلة إلى الحالة الصلبة بدون أن تتبلور عن طريق معالجتها حرارية معالجة خاصة. وعادة تتعرض معظم المعادن لعملية التبلور خلال تبرّدها وتنظّم ذراتها لتشكل نموذجا عالي التنظيم يدعى شبكة بلورية. في حين أن الزجاج المعدني يتشكل خلال نفس العملية في صورة لا بلورية حيث تترتّب بشكل عشوائي (يسمي الزجاج أحيانا بسائل صلب).
وبشكل مغاير للألواح الزجاجية، فالزجاج المعدني لا يكون شفافا، لكن تكوينه يجعله يمتلك خصائص مغناطيسية وميكانيكية متميزة وصلابة عالية.
وذكر البروفسور هاف ناغيل حول هذا الأمر:
«إذا أردنا تصنيف المواد بحسب قابليتها للتحول، نستطيع أن نقول بكل ثقة أنّ الزجاج المعدني لن يدخل ضمن هذا التصنيف. إنّ المواد الزجاجية المعدنية مميزة بشكل كبير أكثر من أي مادة أُخرى».
والآن يحاول هاف نايغل تركيب مادة زجاجية معدنية تحافظ على صلابتها بالإضافة إلى تمتعها بعدم القدرة على التبلور بحيث تقاوم الحرارية العالية لاستخدامها في مكونات الآلات. وقامت بدعم أبحاثه مادياً المؤسسة العلمية الوطنية الأمريكية ودائرة البحث في الجيش الأمريكي.
وكانت أغراض تلك المؤسسات تهدف إلى مادة يمكن استخدامها في المقذوفات الانفجارية قادرة على اختراق الدروع. وبشكل مغاير لمعظم المقذوفات البلورية المعدنية التي تتسطح على الهدف بشكل مشرومي، يرى هاف نايغل أن أطراف الزجاج المعدني لن تنتشر فوق الهدف، بل تبقى متماسكة فتكون ضربتها أكثر حدّة على الهدف.
ويقول «هاف نايغل»:
«ينظر إلى علم المعادن تقليدياً على أنّه الفن الأسود، ومنذ زمن بعيد قام الناس بتركيب الأشياء بدون أن يعرفوا ماهية تركيبها، لذلك فإنّ علم المعادن يقدم مساهمة حقيقية تساعدنا في تصوّر عملية تكون الأشياء وكيف يمكن أن نجعلها تعمل بشكل أفضل».
وأضاف: «جزء مما نقوم به ما زال يدور في نطاق الكيمياء، وهو عملية خلط المواد لمعرفة مقدار جودتها في تكوين الزجاج المعدني، والقسم الآخر من عملنا يتضمن الطبيعة الفيزيائية، فنحن بحاجة لفهم كيفية حصول عملية التبلور لتصميم كتل بحسب المواصفات المرغوبة، لذا فإنّنا نحتاج إلى الكثير من البحث الأساسي على هذه المادة».
ولأنّ المواد الزجاجية المعدنية تفتقد نظام التبلور، ستكون هذه المواد مميزة من الناحية المغناطيسية بالإضافة إلى كونها ستنخفض حرارتها بسهولة بعد القيام بصبها في قوالب، الأمر الذي سيجعلها مطلوبة بشكل كبير في عمليات التصنيع. مع ملاحظة أن عملية صب هذه المواد في قوالب لتكوين كتل كبيرة هي عملية صعبة للغاية، لأنّ معظم المعادن تميل إلى التبلور عندما تبرد. ونحن بحاجة إلى مراعاة تصلّب المعدن قبل حدوث التبلور عن طريق اتباع نظام تبريد معين بقصد تحويله إلى زجاج معدني.
إذا أردنا أن نصنع الزجاج المعدني من معدنٍ نقي كالنحاس أو النيكل فعلينا أن نقوم بإضافة ذرات المعدن بنسبة عالية حتي يصبح الزجاج فوق المشبع بذرات المعدن، وعند التبريد تصبح ذرات المعدن عالقة في الزجاج.
على أيّة حال، تعلّم علماء علم المعادن في خمسينيات القرن الماضي كيفية إبطاء تبلور المعادن عن طريق خلط بعض المعادن مثل النيكل والزيركونيوم. وعندما تمّ تبريد الطبقة السطحية الرقيقة بمقدار مليون درجة في الثانية تمكنوا من الحصول على تركيب الزجاج المعدني لاستخدامها كشرائط رقيقة أو أسلاك أو مساحيق. أما في الوقت الراهن، فقد تمكن العلماء من تركيب حوالي 10 من المواد الزجاجية المعدنية على شكل أعمدة وكتل من خلال جمع أربع أو خمس عناصر ذات ذرات متنوعة الأحجام مع بعضها البعض، الأمر الذي يصعب عملية تبلور الشبيكة في الخليط. وقد تمّ تسويق أحد هذه الكتل الزجاجية المعدنية لاستخدامها في صناعة رؤوس مضارب لعبة الغولف.
هل يمكن للزجاج السماح لنفاذ الضوء دون الحرارة؟
طور باحثان بريطانيان نوعا من الزجاج يمنع نفاذ الحرارة دون أن يمنع نفاذ الضوء، وذلك عن طريق إضافة مادة كيميائية للزجاج تتغير طبيعتها عند وصول الحرارة لدرجة معينة، وتحول دون نفاذ موجات الضوء في نطاق الأشعة تحت الحمراء، وهو النطاق الذي يؤدي إلى الشعور بالحرارة المصاحبة لضوء الشمس.
والمادة الكيميائية التي استعملها الباحثان إيفان باركن وتروي ماننغ من الكلية الجامعية بجامعة لندن، هي ثاني أكسيد الفاناديوم. وهي مادة تسمح – في ظروف الحرارة العادية – بنفاذ ضوء الشمس سواء في النطاق المنظور أو في نطاق الأشعة تحت الحمراء.
ولكن عند درجة حرارة 70 مئوية (تسمى درجة الحرارة الانتقالية) يحدث تغير لتلك المادة، بحيث تترتب إلكتروناتها في نمط مختلف، فتتحول من مادة شبه موصلة إلى معدن يمنع نفاذ الأشعة تحت الحمراء. وقد تمكن الباحثان من خفض درجة الحرارة الانتقالية لثاني أكسيد الفاناديوم إلى 29 درجة مئوية بإضافة عنصر التنغستين.
وذكر الباحثان في مجلة «كيمياء المواد»، أنهما قد توصلا لطريقة فعالة لإضافة ثاني أكسيد الفاناديوم للزجاج خلال عملية تصنيعه، ما يمكن من إنتاجه بتكلفة منخفضة. وباستخدام الزجاج الجديد ينتظر أن يتمكن الفرد من الاستمتاع بضوء وحرارة الشمس معا إلى أن تصل حرارة الغرفة إلى 29 درجة مئوية، وقتها سيعزل الزجاج الأشعة تحت الحمراء، بينما سيظل بالإمكان الإفادة من الضوء المباشر للشمس بدلا من الطرق التقليدية التي تمنع وصول كل من الضوء والحرارة مثل الستائر التي تغطي الشرفات والواجهات.
إن الزجاج الجديد سيحل مشكلة عصرية يواجهها المصممون المعماريون عند تصميم المباني ذات الواجهات الزجاجية، كما سيخفض تكاليف تكييف الهواء التي تبلغ ذروتها في أوقات الصيف الحار. ورغم وجود بعض المشاكل التقنية في طريق الإنتاج التجاري لذلك الزجاج مثل عدم ثبات مادة ثاني أكسيد الفاناديوم على الزجاج وكذلك اللون الأصفر القوي لتلك المادة، فقد ذكر الباحثان أنهما بصدد التغلب على مثل هذه المشاكل التقنية قريبا. وأوضحا أنه لغايات تثبيت ثاني أكسيد الفاناديوم جيدا مع الزجاج ستضاف مادة ثاني أكسيد التيتانيوم. وسيضاف أحد الأصباغ لإزالة اللون الأصفر. وينتظر طرح الزجاج الجديد في المستقبل القريب.
انظر أيضًا
- تاريخ الزجاج
- تشكيل بالنفخ
- صدمة حرارية (خواص المواد)
- الكوارتز
- زجاج حساس للضوء
- معامل انكسار
- زجاج ياقوت الذهب
المصادر
![]() |
في كومنز صور وملفات عن: زجاج |